We're open daily! View holiday hours
Science News
Better Concrete
June 17, 2013
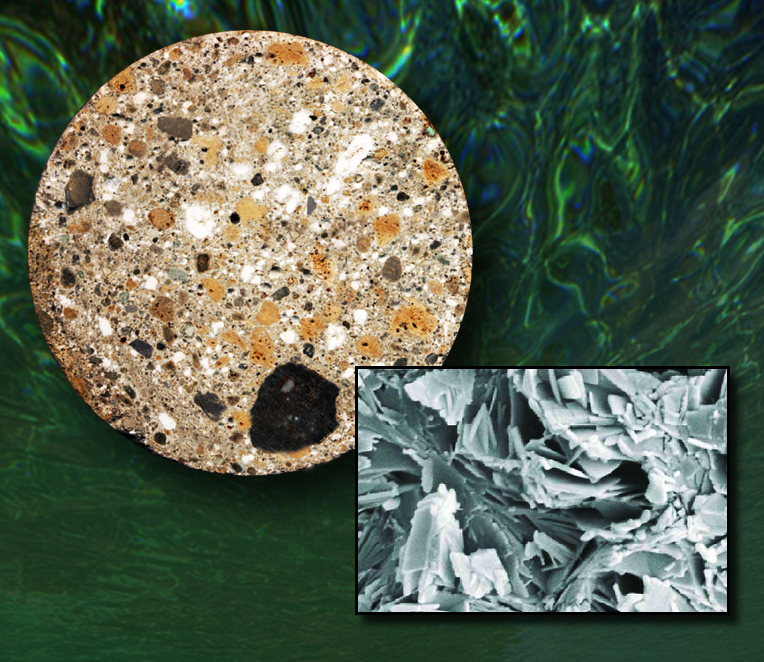
By Molly Michelson
Sometimes to look into the past you need to dig deep—not just physically, but visually, as well. Some of the experiments at the Advanced Light Source (ALS) in Berkeley do just that. With their powerful X-rays they can examine dinosaur blood or determine what killed Napoleon.
Scientists at the ALS recently dug into Roman concrete this way. Remarkably, Roman concrete constructed 2,000 years ago is still strong today, even under rough sea. In contrast, the concrete we manufacture only lasts around 100 years.
Additionally, most of the concrete we produce today has terrible environmental impacts. The process for creating Portland cement, a key ingredient in modern concrete, requires fossil fuels to burn calcium carbonate (limestone) and clays at about 1,450 degrees Celsius (2,642 degrees Fahrenheit). Seven percent of global carbon dioxide emissions every year comes from this activity.
To make a greener, more durable concrete, scientists from King Abdullah University of Science and Technology in Saudi Arabia, working with Berkeley researchers, used spectroscopy at the ALS to examine the Roman concrete and determine its ingredients. Ancient Romans made no secret that volcanic ash was part of the process, but the team also discovered a very rare hydrothermal mineral called aluminum tobermorite (Al-tobermorite) that formed in the concrete, and evidence also suggests the use of seawater in mixing the concrete.
To build underwater structures, Romans mixed lime and volcanic ash to form mortar, and then packed this mortar and volcanic tuff into wooden forms. The seawater instantly triggered a hot chemical reaction. The lime was hydrated—incorporating water molecules into its structure—and reacted with the ash to cement the whole mixture together.
The researchers are now finding ways to apply their discoveries about Roman concrete to the development of more earth-friendly and durable modern concrete. They are investigating whether volcanic ash would be a good, large-volume substitute in countries without easy access to fly ash, an industrial waste product commonly used to produce modern, green concrete. (Fly ash was used in constructing the Academy’s LEED-certified building.)
“Many countries don’t have fly ash, so the idea is to find alternative, local materials that will work, including the kind of volcanic ash that Romans used,” says Berkeley’s Paulo Monteiro, one of the authors on a recent study. “Using these alternatives could replace 40 percent of the world’s demand for Portland cement.”
The ALS shows that by looking into the past, you can solve problems for the future.
Image: Carol Hagen